CIDETEC is a key international player in research and innovation related to surface engineering and polymeric and composite materials. It specialises in processing surfaces and materials through disruptive technologies, ultimately aiming at technological transfer that will ensure the right solution for each customer.
CIDETEC focuses on:
- Developing REACH-compliant* coatings and surfaces that provide multifunctional properties such as corrosion and wear resistance, protection against hydrogen embrittlement or fouling, electromagnetic transparency, customised aesthetics, omniphobicity and conductivity enhancement.
- Developing new innovative, sustainable polymeric materials based on biomass waste, self-healing elastomers, thermoplastic formulations with custom properties, and our own 3R patented technology (Reprocessable, Repairable and Recyclable thermoset composites).
CIDETEC is Spain’s only technological centre specialising in Surface Engineering. Aligned with sustainability and environmental policies, it counts on state-of-the-art equipment and facilities paired with a multidisciplinary team of experts that will help accelerate the company’s innovation process.
In exFan, CIDETEC is the Project Administrative Coordinator. In this role, it´s CIDETEC’s responsibility to organize the meetings and make sure that the cooperation between all the partners is going in the best possible way, in order to achieve the best possible results for the project. Aside from that, they are also involved in the design, testing and characterisation of Heat Exchangers surfaces. CIDETEC will develop by an “Out-of-Bath” approach, surface treatments on Heat Exchangers to improve corrosion resistance and reduce particle accumulation.
*Registration, Evaluation, Authorization and restriction of Chemicals (REACH)
Advanced Drivetrain Technologies (ADT), the Austrian engineering firm, is dedicated to advancing environmentally friendly and sustainable drivetrains. Specializing in cutting-edge propulsion and energy systems, with a focus on thermal management design and gear optimization, ADT actively engages in national, trans-national, and international funded research projects within the aviation sector, aligning with the objectives of the European Green Deal.
In the exFan project, ADT plays a pivotal role as the technical coordinator, leading in systems engineering and thermal management design. Beyond theoretical contributions, ADT has established a robust infrastructure to facilitate seamless communication among project partners. This collaborative space serves as a platform for defining essential functions, interfaces, and requirements crucial to the successful development of the exFan project.
ADT takes the lead in the multidisciplinary development process, which will produce the concept of the exFan. ADT also supports TUW in finding the right boundary conditions of the exFan. Together, they explore various operating conditions to derive invaluable insights that will inform the mission- and functional requirements of the propulsion system. The collective efforts of ADT and its partners aim to make a significant impact on the success of the exFan project, furthering the aviation industry's commitment to sustainability.
The role of TU Wien (TUW) is the layout and design of exFan’s heat propulsion system. During the exFan project, TUW focuses its research to optimize the utilization of waste heat, provided by fuel cells, using the Meredith effect to propel a fuel cell powered aircraft and improve the overall efficiency. In later stages of the project TUW is tasked to conduct testing and perform simulations to proof the concept of the developed propulsion system. Furthermore, as part of the board of coordinators in the role of research coordinator, TUW is responsible to supervise all partners involved in the development and evaluation of the heat propulsion system and to lead the development of exFan together with ADT and Cidetec.
The Aircraft Systems Research Group at TU Wien was established in 2021 with funding from the Austrian Federal Ministry for Climate Action, Environment, Energy, Mobility, Innovation and Technology (BMK), TU Wien and co-financing industrial partners within the framework of an endowed professorship at TU Wien. Headed by Univ. Prof. Dr.-Ing. Martin Berens the research group seeks to increase Austria’s scientific output in the field of aeronautics, with an emphasis on technologies to eventually achieve climate neutral flight.
The Aircraft Systems Research Group focuses on the following topics:
- Integration of electric propulsion technologies: systems for hydrogen storage and processing (CGH2/LH2), fuel cells, accumulators, engines, transmissions, propulsors,
- Efficient thermal management and integration of thermal management systems into the airframe,
- Aerodynamics and aeroacoustic simulations of aircraft systems,
- Validation of numerical models based on tests with scaled components,
- Component optimisation and system integration, as well as
- Development of reduced-order models and corresponding software tools for use in aircraft concept and system simulation environments.
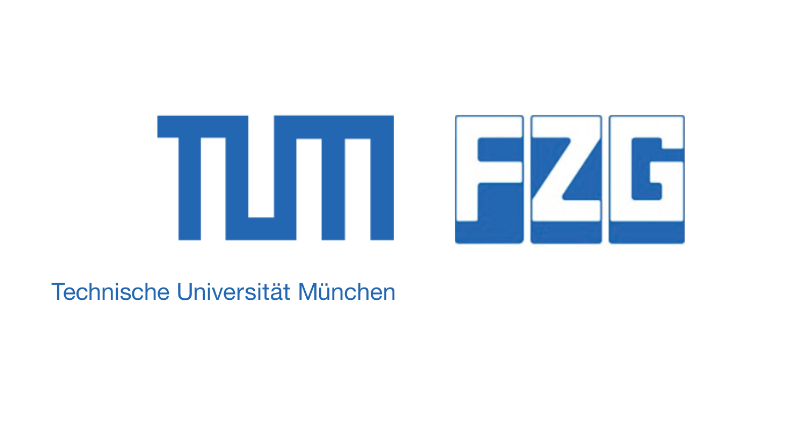
The Institute of Machine Elements at Technische Universität München, also called "Gear Research Center (FZG)", has been the competence center for mechanical drive technology with comprehensive facilities for examination and testing of machine elements, such as gears, bearings, synchronizations, and couplings. Based on the research results developed here during the past decades, the FZG is the leading international research institute for gears and transmissions today. The development of methods and tools of reliable determination of fatigue life, efficiency, and vibration characteristics of gears and transmission elements is in the focus of the research activities at the FZG. The implementation of the research is carried out in close cooperation with the industry, funded either through public research funding or industrial community research or direct industrial commission.
Within exFan, FZG supports the powertrain's concept phase with knowledge of the design of high-speed electromechanical powertrains. This includes foremost the gearbox, the electric engine, and thermal management, which connects all active components and allows for thrust increase by the heat exchanger. The exFan project aims for a high-power density of the powertrain. Therefore, a small-sized high-speed electric machine is combined with a compact gearbox, which reduces speed according to the fan's demands. In this manner, FZG leads gearbox-related topics and oversees the final gearbox concept. To finally evaluate generated thrust versus the drag from the heat exchanger, FZG oversees the functional system verification. Additionally, FZG is intensely involved in transferring the gained knowledge to education.
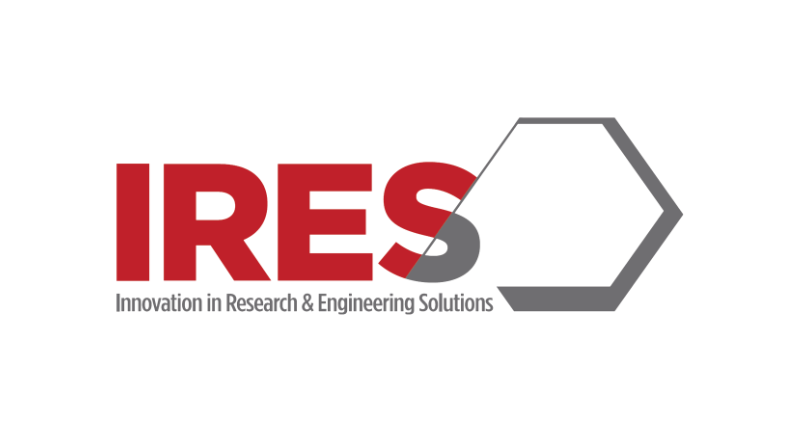
IRES is an independent Belgian consulting company (SME). IRES has a core business and wide experience in the fields of Life Cycle Assessment (LCA) & Life Cycle Costing (LCC), Exposure and Risk Assessment (hazard and exposure scenarios), Data Management Plan (DMP), Machine learning and Data analysis. Through its international network, IRES supports the development of innovative technologies and products.
IRES will assess the potential environmental impacts and evaluate the overall environmental performance of the new exFan concept towards the aviation industry's commitment to action on climate change.
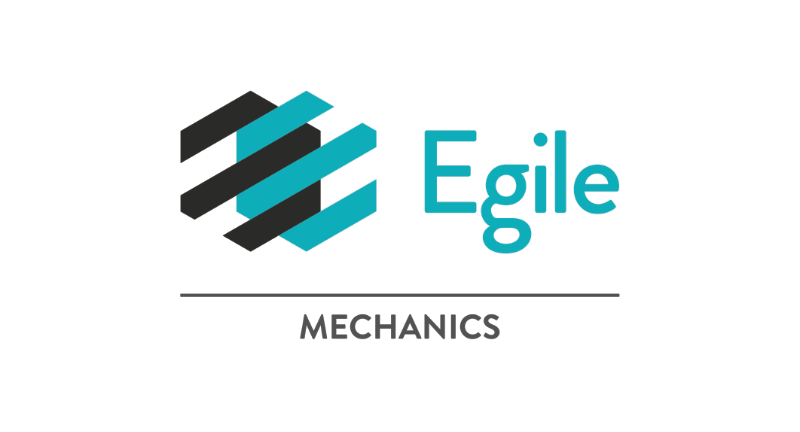
EGILE is a leading organization dedicated to the development and manufacturing of crucial components or systems for aircraft, helicopters, or drones. Operating through three (3) distinct business units, each specialized in technology or market segments, namely Aero Transmissions, Aero Engines, and Aero Systems, EGILE is committed to providing comprehensive support to large OEMs.
With a core focus on projects that are challenging to outsource and emerging technological advancements, EGILE serves as a viable alternative to in-house production of intricate components or complex systems. Their specialized expertise enables them to deliver swift solutions during the development phase and maintain competitiveness throughout mass production stages.
Renowned for their proficiency, EGILE not only offers innovative technological solutions but also plays a pivotal role in enhancing products and processes in long-term projects. Their commitment to excellence, coupled with a specialist profile, positions them as a reliable collaborator for large OEMs, contributing to the overall advancement of aerospace technologies.
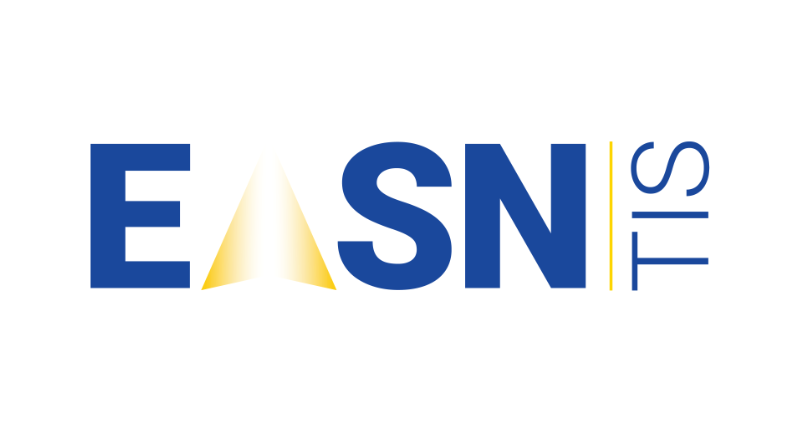
EASN-Technology Innovation Services (EASN-TIS), a dynamic Belgian SME, stands as a key player in aeronautics and air transport research. Born out of the support from the EASN Association, EASN-TIS serves as a crucial bridge, actively participating in research projects and maintaining strong connections through the extensive EASN database. With a focus on collaborative endeavors, EASN-TIS plays a pivotal role in crafting successful research consortia by identifying and bringing together the most relevant partners from academia, industry, and major research organizations, both nationally and internationally.
Within the exFan project, EASN-TIS takes on multifaceted responsibilities. Spearheading a tailored dissemination and communication strategy, it ensures widespread adoption of project results, regularly publish achievements, and enhance societal awareness. EASN-TIS also manages Intellectual Property Rights (IPR) positioning, develops business plans for joint and individual exploitation, and facilitates seamless information exchange with CAJU & CH Partnership. Additionally, a succinct Data Management Plan is in place, emphasizing open data principles while respecting confidentiality and data protection. EASN-TIS's comprehensive role ensures the success and impactful outcomes of the exFan project.
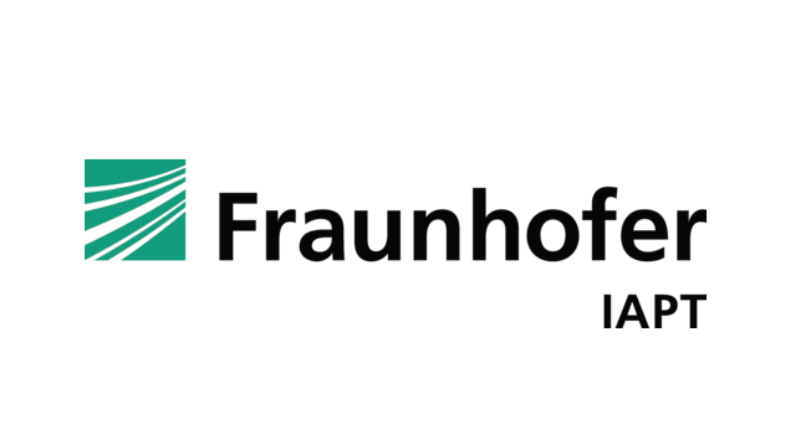
The Fraunhofer Research Institution for Additive Manufacturing Technologies (IAPT) in Hamburg, Germany, specializes in Additive Manufacturing and focuses on next-generation topics such as Mobility, Energy, Life Science, and Security.
In the exFan project, the IAPT develops and integrates new heat exchangers to cool the fuel cell and recover heat for the propulsion system. Additive manufacturing allows for design freedom and lightweight parts, enabling the creation of customized cooling channels with improved heat dissipation. The IAPT also provides support in surface design for corrosion resistance and manufactures prototypes for the validation of simulation results and performance evaluation.
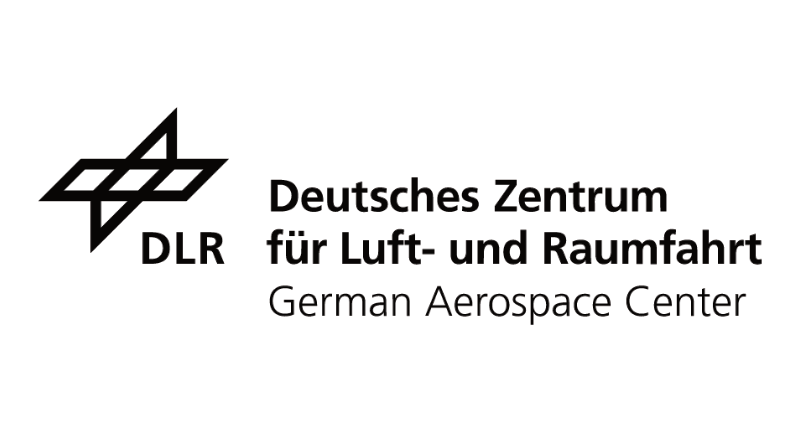
The German Aerospace Center (German: Deutsches Zentrum für Luft- und Raumfahrt e.V., abbreviated DLR, literally German Center for Air- and Spaceflight) is the national center for aerospace, energy, and transportation research of Germany, founded in 1969. It is headquartered in Cologne with 35 locations throughout Germany. The DLR is engaged in a wide range of research and development projects in national and international partnerships. The DLR acts as the German space agency and is responsible for planning and implementing the German space programme on behalf of the German federal government. As a project management agency, DLR coordinates and answers the technical and organizational implementation of projects funded by several German federal ministries. As of 2020, the German Aerospace Center had a national budget of €1.348 billion.
DLR is organized in institutes, and in exFan project the Institute of Propulsion Technology is mainly involved. The institute focuses its research on the development and virtualization of high-performance and environmentally friendly aircraft engines and power plant turbines. We investigate the evaluation and validation of innovative propulsion concepts such as the use of hydrogen and alternative aviation fuels in gas turbines and aircraft engines, on highly efficient turbo components and on low-emission combustors.
The role of DLR, which in the exFan project is represented by the Fan and Compressor department, is to design and explore different fan concepts in conjunction with heat release in the bypass channel. The operational implications of the fan will be explored, along with exploring the options to maximize thrust to power ratio and the interaction with the heat exchanger.
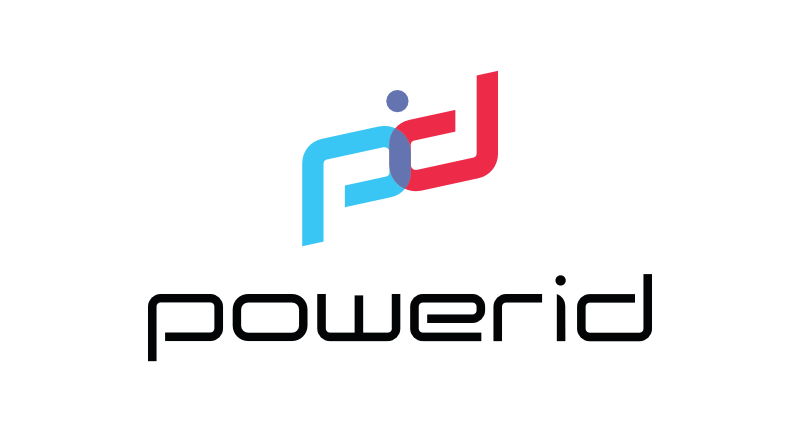
Power I.D. GmbH, headquartered in Stuttgart, Germany, stands out as a leading technology and engineering provider with an impressive legacy of over 50 years in the dynamic realms of e-mobility and high voltage system development. Renowned for its prowess in crafting electric drives, batteries, and scalable mass production solutions, Power I.D. is a trusted partner for OEMs, suppliers, engineering entities, and consultants alike.
At the heart of its mission is a steadfast focus on innovation, where Power I.D. champions ideas and holistic solutions tailored for mass production. This commitment extends to the digital forefront of e-mobility, positioning the company as a supportive force through its in-house team and collaborative efforts with seasoned consultants and project managers. Areas of specialization span the technological spectrum, covering electric drive development, seamless vehicle integration, rigorous validation and testing procedures, and refined processes and methods such as change management, requirements management, design to cost, testing strategy, and supplier strategy and nomination.
In the organizational and leadership domains, Power I.D. excels in corporate strategy, transformation initiatives, organizational development, project management, and task force management. Notably, the company takes a pivotal role in the groundbreaking exFan project. Here, Power I.D. assumes responsibility for the specification and simulation of the hybrid system, showcasing its expertise in intricately incorporating fuel cells and high voltage batteries into this innovative venture. The exFan project underscores Power I.D.'s commitment to pushing the boundaries of technology and engineering in the pursuit of cutting-edge solutions for the future of mobility.