exFan aims to investigate and develop a concept for a novel thrust generating heat dissipation and recuperation system, called heat propulsor. This goal assumes that there is about 50% of waste heat of a fuel cell which needs to be dissipated and can be used to produce additional thrust. The underlying concept of the goal is the so-called Meredith effect, which occurs when air flowing through a duct is heated by a heat-exchanger or radiator in forward flight. The duct is designed in a way that the air flowing into the duct meets drag resistance from the radiator surface and is compressed due to the ram air effect. When the air flows through the radiator it is heated and increases its volume. The hot, pressurized air then exits through the exhaust duct, which is shaped to be convergent, i.e. to narrow towards the rear. This accelerates the air backwards and the reaction of this acceleration against the installation provides a small forward thrust. To design such a device for a fuel cell powered geared electric fan propulsion system of mega-watt class and include it inside the propulsion system is one of key milestones of the exFan project.
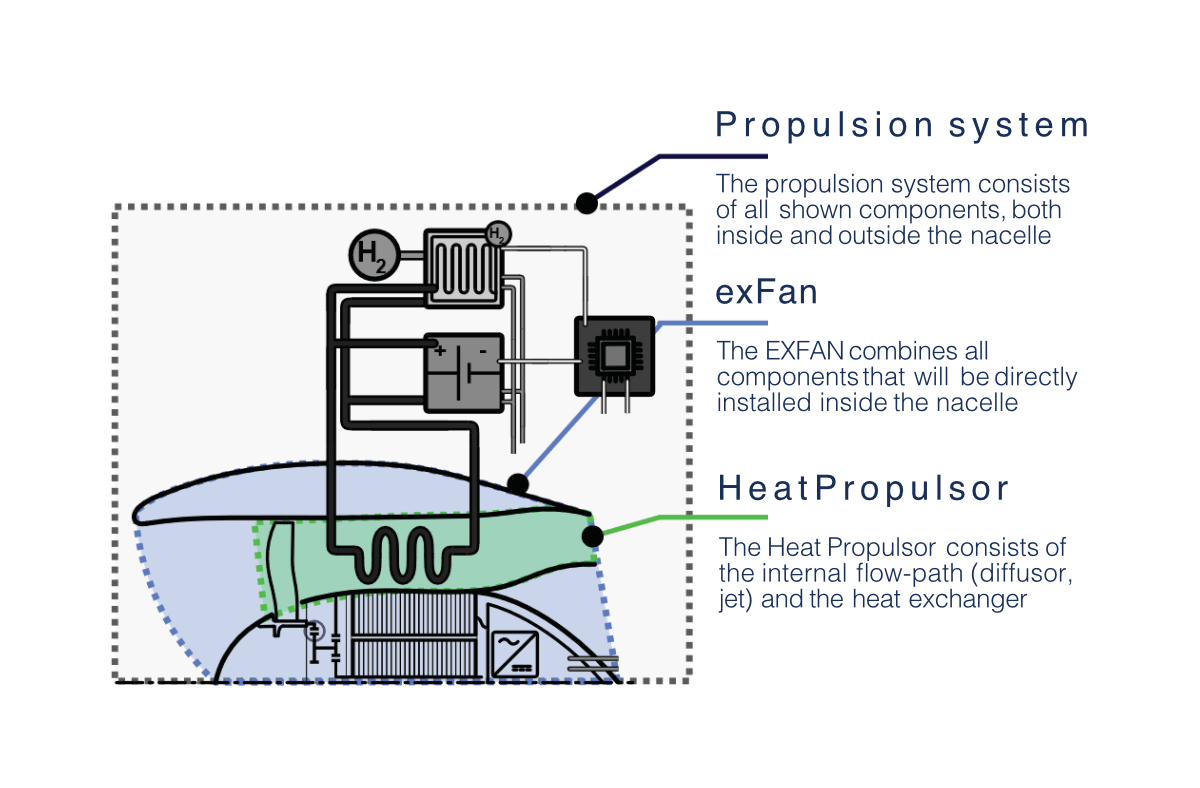